A lot has been made of the Focus RS Ecoboost 2.3 head gasket failures. It seems to be an issue that has occurred in both modified and unmodified vehicles. I am not certain what percentage of vehicles are affected. However we have spent significant time looking at the mechanics of the failure and wanted to share this with our customers and community.
The Focus RS uses a multi layer steel (MLS) head gasket. This is a very capable method for sealing the block to head interface. This multilayer gasket is enhanced by an elastomer that further helps seal critical areas.
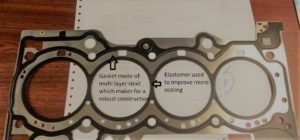
The Focus RS 2.3 Ecoboost engine block is an open deck design. This means that the cylinders are not attached to the outside of the block structure at the sealing surface of the head gasket. This space is filled with engine coolant.
The head and block are secured to each other using torque to yield bolts (which do not require re-torquing the head fasteners after the engine is heat cycled). In spite of this there is inevitable movement between the two sealing surfaces. The two types of movement are vertical movement (which is what causes head lift and a sudden gasket failure) as well as lateral movement. This lateral movement is of most interest in this situation. Minute lateral movement causes what is called gasket fretting/scrubbing. There are two mechanisms that cause this lateral movement:
- Thermal deformation. As the engine is brought through a range of temperatures (within normal operation), the expansion and contraction of the head and block cause this lateral movement between the two interfaces. The movement caused by this is however low cycle, as the engine is warmed up and cooled down relatively few times compared to the next mechanism.
- The most relevant mechanism for lateral movement is due to cylinder firing. When a cylinder fires, it applies pressure on the open deck cylinder structure. This in turn causes this minute movement between the two interfaces scrubbing them at a high rate.
The result of this scrubbing is material loss from the head gasket, block, or head. Over time, the seal between the block and head can fail. The area where it will fail first is the area with: the highest movement, the highest contact pressure, and the least sealing material available.
The area of highest lateral movement for the Focus RS is between the cylinders.
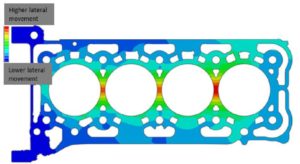
The area of highest contact pressure is around the cylinders (because this is where the combustion pressure is highest and needs the best seal). This is by design.
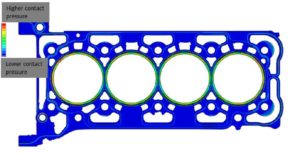
The area that will inevitably experience the highest wear rate will be between the cylinders. Manufacturing discrepancies, vehicle use, temperature fluctuations and other factors will influence whether a failure will occur on a vehicle and if so when.
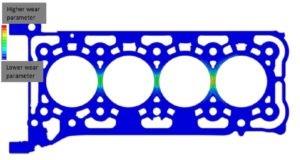
There are two methods to reduce this scrubbing wear. One is to stiffen the block structure. When rebuilding an engine for example, using the closed deck 2.0 Ecoboost block is an attractive option. However, Ford could not use this block in production and I am certain there are good reasons for this; likely related to emissions certification.
The second method, and what is being implemented as a fix is to redesign the head gasket.
Below is an image of a failed Focus RS gasket. A few things to note:
- There is a very high wear rate of the elastomer (black section) between the cylinders. This is where the gasket has failed. You can see that it is almost completely missing in these areas.
- Notice how thin the sealing area is between the cylinder overall.
- Looking carefully you will notice that the are two holes in gasket between the cylinders marked on the image below.
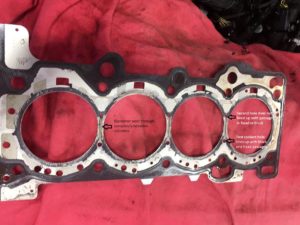
Now let’s have a look at the block. You can see there is a very smallcoolant hole on the exhaust side. This hole lines up with one of the holes in the failed head gasket. You can also see a trail of coolant marking on the block surface leading to the second hole. This shows there is no elastomer between the cylinders on the original head gasket.
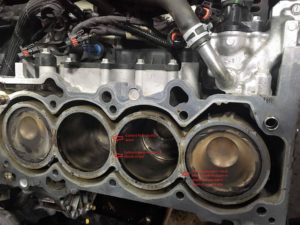
Looking at the head, you can see that the first hole on the head gasket lines up with a coolant passage. The second hole, however does not line up with any coolant passage. Once again, the head shows that coolant was found in the area between the cylinders but this was a closed path. Overall the cylinder sealing area was very narrow and the head gasket failed after a number of miles.
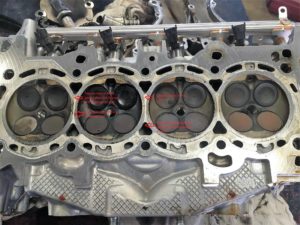
When the car was brought to the dealer, it was repaired with the head gasket shown below. There are some very important changes in the area between the two cylinders on the updated gasket.
- The second deadheaded hole is no longer present
- The entire area between the cylinders is now coated in elastomer. This will increase the sealing surface area and better distribute the clamping force in this critical area. This will in turn reduce the fretting/scrubbing failure of the head gasket.
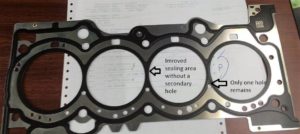
The latest gasket part number is G1FZ-6051-C and this is what dealers are replacing failed gaskets with on vehicles that experience this failure. I am not sure at what point the factory engines have received this latest gasket part number. The only indication I was given was that this part number was available to service centers sometime between 3/27/17 and 8/10/17. Again, this says nothing regarding when this change was made to vehicles coming out of the factory.
I hope this clears up some of the confusion around these head gasket failures and what is causing them. The symptoms of failure are:
- Loss of coolant.
- Misfires, especially on a cold start and rough running.
- Coolant fouled/wet spark plugs.
If you experience these symptoms, take the car in to Ford for the fix. Otherwise, enjoy the RS! It is not the only car in history to experience difficulties with head to block sealing. High output, low emissions, small displacement engines like the RS are a challenge to engineer and can have some teething issues; but at the same time we can all agree that fun behind the wheel was certainly well engineered!
The Stratified Team
Photo credit:
Brewer, T. and Chen, X., “Cylinder Head Gasket Fretting/Scrub Mechanism Investigation and Analysis Procedure
Developments,” SAE Technical Paper 2017-01-1091, 2017, doi:10.4271/2017-01-1091.